The Welding Process of Aluminum Alloy Frames for Electric Bicycles
aluminum frame welding, structural strength in e-bike frames, lightweight e-bike design.challenges in aluminum welding, oxide layer removal, hot cracking prevention.TIG welding aluminum, precision welding for e-bikes, clean welds.MIG welding aluminum, high-volume e-bike production, efficient welding techniques.laser welding for e-bikes, seamless aluminum welding, advanced frame welding.
WINboard Electric Mobility
3 min read
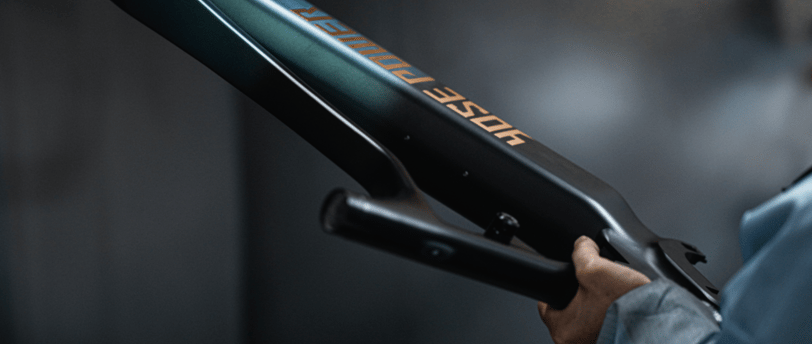
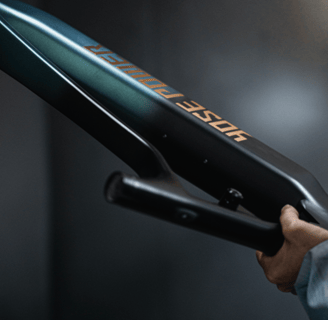
The Welding Process of Aluminum Alloy Frames for Electric Bicycles
Welding aluminum alloy frames for electric bicycles is a critical step in manufacturing that determines the frame's strength, durability, and long-term reliability. Aluminum alloys, known for their lightweight and corrosion-resistant properties, are an ideal material for e-bike frames, but they require precise welding techniques to handle their unique characteristics. Among these, post-weld heat treatment is essential to ensure proper penetration and weld integrity.
This article will provide an in-depth exploration of aluminum alloy frame welding, covering preparation, techniques, challenges, post-weld heat treatment, and quality assurance, while incorporating SEO-friendly keywords for optimal search visibility.
The Importance of Welding in Aluminum Alloy Frames
1. Structural Strength
Welding is the backbone of the frame’s structural integrity, joining multiple components to create a seamless and robust whole. High-quality welds ensure that the frame can withstand the stresses of urban commuting, off-road cycling, or delivery operations.
2. Lightweight and Durable Design
Aluminum welding techniques optimize the material's lightweight properties while maintaining the durability needed for safety and performance.
3. Preparing for Long-Term Use
Proper welding and post-weld processes, such as heat treatment, prevent issues like cracking or weak welds, extending the lifespan of the e-bike frame.
Challenges in Welding Aluminum Alloy Frames
1. High Thermal Conductivity
Aluminum dissipates heat quickly, making it challenging to maintain consistent weld penetration without overheating or deforming the material.
2. Oxidation
Aluminum forms a natural oxide layer that must be removed before welding to ensure proper fusion and penetration.
3. Risk of Cracking
The material's high shrinkage rate and low melting point make it prone to hot cracking during and after welding.
Common Welding Techniques for Aluminum Frames
1. TIG Welding (Tungsten Inert Gas)
TIG welding is the preferred method for aluminum frames due to its precision and clean results.
Advantages:
Excellent control over heat and weld pool.
Produces aesthetically smooth and strong welds.
Applications:
Used for intricate joints and thin-walled tubing.
2. MIG Welding (Metal Inert Gas)
MIG welding is faster and better suited for thicker materials, making it ideal for large-scale production.
Advantages:
Speed and efficiency.
Reliable for thicker sections of the frame.
Applications:
Commonly used in less intricate sections or high-volume manufacturing.
3. Laser Welding
Laser welding is a high-precision, modern technique that minimizes heat distortion and creates nearly invisible seams.
Step-by-Step Welding Process
1. Frame Preparation
Cleaning: Removal of the oxide layer using wire brushes or chemical solutions.
Alignment and Fixtures: Frames are clamped securely to maintain accuracy during welding.
2. Preheating
Preheating the aluminum to 150–200°C reduces thermal shock and prevents cracking during welding.
3. Welding Execution
TIG or MIG Welding: Precise control over the welding process ensures proper fusion.
Multi-Pass Welding: Used for thicker sections to ensure deep penetration and strong bonds.
Post-Weld Heat Treatment: Ensuring Weld Safety
1. The Importance of Heat Treatment
After welding, aluminum frames undergo post-weld heat treatment (PWHT) to enhance the strength and safety of the weld joints. This critical step ensures that every weld seam is properly penetrated and free from internal stress or weaknesses.
2. Benefits of Post-Weld Heat Treatment
Stress Relief: PWHT eliminates residual stresses caused by rapid cooling during welding.
Improved Ductility: The process restores the aluminum alloy’s flexibility, reducing the risk of cracking under stress.
Enhanced Penetration: Ensures weld seams are uniformly fused with no voids or weak points.
3. Heat Treatment Techniques
Solution Heat Treatment: The frame is heated to a specific temperature and rapidly quenched to improve mechanical properties.
Aging Treatment: Slowly heating the frame to moderate temperatures enhances its durability.
Quality Assurance in Aluminum Frame Welding
1. Non-Destructive Testing (NDT)
Techniques like ultrasonic or X-ray testing are employed to detect internal defects without damaging the frame.
2. Visual and Dimensional Inspection
Inspectors evaluate weld seams for uniformity, penetration, and aesthetic quality.
3. Stress Testing
Frames undergo stress testing to ensure they meet the safety standards for various riding conditions.
Automation and Advanced Welding Technology
1. Robotic Welding Systems
Automated welding increases precision, consistency, and production efficiency, reducing human error in high-volume manufacturing.
2. Advanced Welding Materials
The use of high-quality filler materials and specialized alloys minimizes cracking and ensures superior weld strength.
Environmental Considerations in Welding
1. Energy-Efficient Welding
Modern welding equipment is designed to optimize energy use, reducing the carbon footprint of production.
2. Aluminum Recycling
Recycled aluminum is increasingly used in manufacturing, contributing to a circular economy.
Conclusion
The welding of aluminum alloy frames for electric bicycles is a highly specialized process that combines advanced techniques, rigorous preparation, and post-weld heat treatment to ensure safety, durability, and performance. Manufacturers like WUXI WINBOARD INTELLIGENT TECHNOLOGY integrate modern technologies and sustainability practices to produce world-class e-bike frames.
With precision welding and post-weld heat treatment as cornerstones of quality, aluminum alloy frames are set to continue driving innovation in the electric mobility industry.